對于工業(yè)核心板的生產(chǎn),壓配是最重要的過程。生產(chǎn)過程中存在許多值得研究和討論的問題,例如:銅箔起皺,壓接層局部偏斜,樹脂空隙,白邊白角,分層起泡,厚度不均等。而為了解決上述問題,必須清楚地了解主要材料(內(nèi)芯板,PP)和壓力機的控制點,并熟悉其特性。那么, 下面就由小編為大家介紹一下吧!
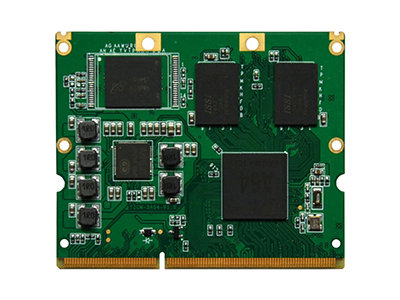
隨著多層板的水平越來越高,內(nèi)芯板越來越薄,水平褐變過程逐漸采用垂直發(fā)黑過程,這證實了內(nèi)芯板的褐變效果是否滿足要求。從三個方面來看:微蝕刻,耐酸時間,褐變張力。
芯板壓制的主要材料有哪些,內(nèi)芯板被蝕刻以形成內(nèi)層圖案的多層芯板稱為內(nèi)層芯板,并且在壓制之前必須對內(nèi)層芯板進行棕色(黑色)處理,以增加其表面。內(nèi)層銅箔。粗糙度使得PP片材流膠在壓制過程中完全粘合到銅表面上,從而增加了PP與銅表面之間的粘合力。
一,工業(yè)核心板的沖壓設(shè)備
1.熱壓類型:
根據(jù)加熱方式的不同,主要可分為:
1電熱加熱:這是一種較早的加熱方法,但是由于提升溫度不穩(wěn)定,因此很少使用;
2煤油熱加熱:熱介質(zhì)油通過鍋爐加熱,熱量通過熱介質(zhì)油傳遞到壓機。由于提供的熱量穩(wěn)定,因此易于控制溫度的上升和下降。目前,大多數(shù)壓機都使用這種加熱方法。
2.壓壓方式:
目前,大多數(shù)壓力機使用液壓加壓,壓力源是從下至上的圓筒形。
3.控制點:
1真空:壓機啟動后,在開始壓機前先抽真空,以免在壓機過程中殘留氣泡;
2時間:各階段的溫度和壓力斜率及保持時間,主要影響加熱速率和固化時間;
3壓力:生產(chǎn)板上每個階段的壓力主要影響生產(chǎn)板上的流膠和應(yīng)力釋放;
4溫度:每個階段的壓力機熱板溫度主要影響生產(chǎn)板的實際溫度;
二,工業(yè)核心板的預(yù)浸料(PP):
1.組成:
常用的PP片材主要由環(huán)氧樹脂和玻璃纖維組成;
2.主要基本物理性能:
1膠量RC%:環(huán)氧樹脂的比例,可以根據(jù)IPC-TM-650 2.3.16的測試方法進行測試;
2膠凝時間GT:測試B級PP片材在170℃下完成C級固化所需的時間,可以根據(jù)IPC-TM-650 2.3.18的測試方法進行測試;
3揮發(fā)物V.C%:浸漬后測試PP片材中溶劑的殘留量,可根據(jù)IPC-TM-650 2.3.19的方法進行測試;
3.功能:
1作為與芯板和芯板,芯板和銅箔結(jié)合的介質(zhì);
2阻抗控制:提供可以提供合適絕緣層的厚度;
4.規(guī)格:
當(dāng)前,使用的主要PP片材為106、1080、3313。,2116、1506和7628。不同規(guī)格和相同規(guī)格,不同膠水量和不同壓機厚度的PP片材。
5.儲存條件:
濕度:≤50%RH;
溫度:≤5°C:可保存180天; 20±2℃可保存90天;
三,工業(yè)核心板的壓后質(zhì)量重點:
1.生產(chǎn)板的可靠性:
1熱應(yīng)力:測量生產(chǎn)板的耐熱性,測試方法:熱沖擊(288±5℃,浸錫3次,10秒/次);
2TG;測量生產(chǎn)板的PP是否完全固化,測試方法:IPC-TM-650 2.4.25 DSC
3剝離強度:測量生產(chǎn)板上銅箔和PP的粘合強度。測試方法:IPC-TM-650 2.4.8
2.厚度:
1個切片用于測量介電層的每一層的厚度;
2用測厚儀測量板邊緣的厚度和板的厚度,一般測量5點或9點;
3.外觀:無凹坑,銅箔皺紋,白色邊緣和白色角
以上就是,小編為大家介紹有關(guān)于工業(yè)核心板PCB技術(shù)研發(fā)及介紹要點,希望大家看完這篇文章能夠有所了解,如果大家還有不懂的,歡迎大家來咨詢我們。